
Teknik Jitu Ala TPM Eliminasi Breakdown Failure merupakan bahasan untuk kesempatan kali ini. Kita akan membahas tentang teknik jitu ala TPM yang dapat membantu mengeliminasi breakdown failure atau kegagalan peralatan. Bagi perusahaan manapun, downtime akibat breakdown merupakan masalah yang serius. Selain mengganggu produktivitas, downtime juga berpotensi menyebabkan kerugian finansial. Oleh karena itu, penting bagi kita untuk mengetahui teknik-teknik yang dapat diterapkan melalui pendekatan TPM (Total Productive Maintenance) guna mengatasi masalah ini.
Preventive Maintenance
Perawatan pencegahan, atau preventive maintenance, adalah teknik yang sangat penting dalam menjaga kinerja optimal peralatan di suatu perusahaan. Dengan menjadwalkan perawatan terjadwal dan rutin, perusahaan dapat mencegah terjadinya kegagalan yang tak terduga dan menghindari dampak negatifnya.
Salah satu manfaat utama dari perawatan pencegahan adalah kemampuannya untuk mengidentifikasi masalah potensial sebelum mereka berkembang menjadi kegagalan yang lebih serius. Dengan melakukan perawatan secara berkala, perusahaan dapat melakukan pemeriksaan rutin terhadap peralatan mereka. Hal ini memungkinkan untuk mendeteksi tanda-tanda awal masalah, seperti ausnya komponen atau perubahan dalam kinerja peralatan. Dengan mengidentifikasi masalah tersebut, tindakan perbaikan dapat dilakukan sebelum kegagalan yang lebih besar terjadi.
Selain itu, perawatan pencegahan juga membantu memperpanjang umur pakai peralatan. Dengan menjaga peralatan dalam kondisi terbaiknya melalui perawatan yang terjadwal, risiko kerusakan dan keausan berlebihan dapat dikurangi. Komponen yang aus dapat diganti secara tepat waktu, sehingga mencegah terjadinya breakdown dan memperpanjang masa pakai peralatan tersebut. Hal ini secara langsung berdampak pada efisiensi operasional dan biaya yang lebih rendah dalam jangka panjang.
Selain itu, perawatan pencegahan juga dapat meningkatkan keamanan di tempat kerja. Dengan melakukan pemeriksaan teratur pada peralatan, risiko kecelakaan yang disebabkan oleh kegagalan peralatan dapat dikurangi. Misalnya, pemeriksaan terjadwal pada sistem keselamatan seperti alarm kebakaran atau pemadam kebakaran memastikan bahwa peralatan tersebut berfungsi dengan baik ketika dibutuhkan. Hal ini membantu menciptakan lingkungan kerja yang lebih aman bagi para karyawan.
Terakhir, perawatan pencegahan juga dapat meningkatkan kehandalan produksi. Downtime akibat breakdown peralatan dapat berdampak negatif pada produktivitas perusahaan. Dengan menjadwalkan perawatan terjadwal, perusahaan dapat mengurangi risiko kegagalan yang tak terduga dan downtime yang tidak diinginkan. Peralatan yang bekerja dengan baik dan konsisten membantu menjaga kelancaran proses produksi, meningkatkan efisiensi, dan memenuhi kebutuhan pelanggan dengan lebih baik.
Perawatan pencegahan merupakan teknik jitu dalam TPM yang sangat penting untuk menghindari kegagalan peralatan yang tak terduga. Dengan menjadwalkan perawatan terjadwal dan rutin, perusahaan dapat mengidentifikasi masalah potensial, memperpanjang umur pakai peralatan, meningkatkan keamanan, dan meningkatkan kehandalan produksi. Jadi, mari kita terapkan perawatan pencegahan dengan baik dalam operasional perusahaan kita agar dapat mencapai kinerja optimal dan kesuksesan jangka panjang.
Autonomous Maintenance
Pemeliharaan mandiri atau autonomous maintenance adalah teknik yang melibatkan karyawan dalam perawatan harian peralatan di tempat kerja. Konsep ini didasarkan pada prinsip bahwa karyawan adalah orang yang paling dekat dengan peralatan dan memiliki pemahaman yang mendalam tentang operasional sehari-hari. Dengan melibatkan karyawan dalam perawatan, perusahaan dapat mengoptimalkan upaya perawatan dan mengurangi risiko breakdown.
Salah satu aspek penting dari pemeliharaan mandiri adalah memberdayakan karyawan untuk mengenali tanda-tanda awal masalah pada peralatan. Karyawan diajarkan untuk memperhatikan perubahan dalam suara, getaran, atau kinerja peralatan secara keseluruhan. Dengan pemahaman ini, mereka dapat mengidentifikasi masalah yang muncul dan mengambil tindakan perbaikan sebelum kegagalan yang lebih serius terjadi. Dengan demikian, perusahaan dapat mengurangi downtime yang tidak diinginkan dan mengoptimalkan kinerja peralatan.
Selain itu, pemeliharaan mandiri juga meningkatkan partisipasi karyawan dalam menjaga peralatan. Karyawan merasa memiliki tanggung jawab terhadap peralatan yang mereka gunakan dan merawat. Mereka diberikan pelatihan untuk melakukan pemeriksaan rutin, membersihkan peralatan, dan melakukan tindakan perbaikan sederhana. Hal ini tidak hanya mengurangi beban tim perawatan khusus, tetapi juga menciptakan rasa kepemilikan dan kepedulian terhadap peralatan.
Teknik pemeliharaan mandiri juga membantu meningkatkan pengetahuan dan keterampilan karyawan. Melalui pelatihan dan pembelajaran langsung dalam merawat peralatan, karyawan menjadi lebih terampil dalam mengoperasikan, memantau, dan merawat peralatan dengan baik. Pengetahuan ini tidak hanya berlaku untuk pekerjaan mereka saat ini, tetapi juga dapat mereka terapkan di masa depan. Hal ini memberikan manfaat jangka panjang bagi perusahaan dalam mengembangkan tenaga kerja yang terampil dan mandiri.
Terakhir, pemeliharaan mandiri menciptakan budaya perawatan yang proaktif di perusahaan. Dengan melibatkan semua karyawan dalam perawatan, perusahaan menggabungkan pengetahuan dan pengalaman kolektif mereka untuk meningkatkan keandalan peralatan. Budaya perawatan yang proaktif mendorong identifikasi masalah secara dini, tindakan perbaikan segera, dan pencegahan kegagalan yang tidak diinginkan. Hal ini secara langsung berkontribusi pada pengurangan downtime dan peningkatan efisiensi operasional.
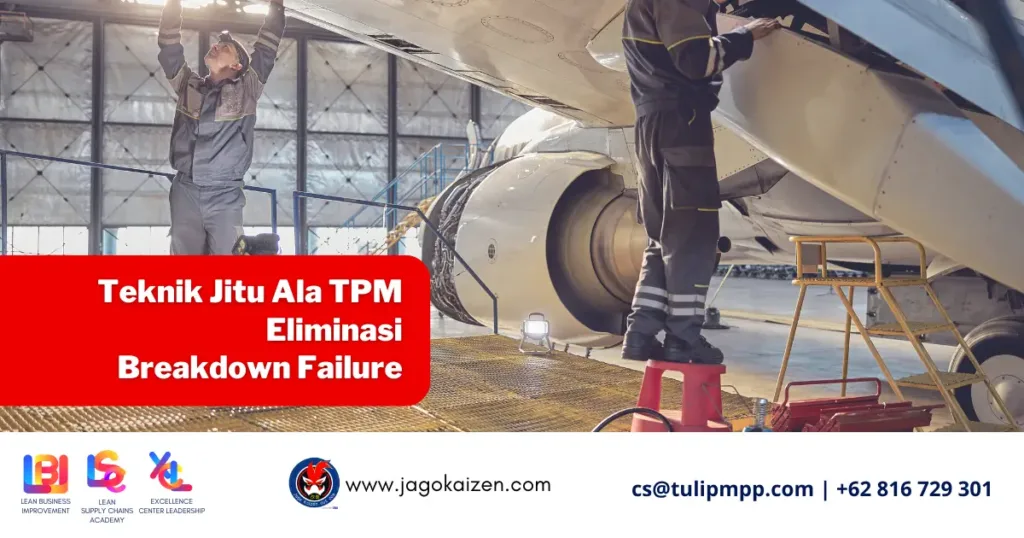
Failure Analysis
Analisis kegagalan, atau failure analysis, adalah suatu proses penting dalam upaya perusahaan untuk mengatasi masalah breakdown peralatan. Dengan melakukan analisis mendalam terhadap kegagalan, perusahaan dapat memahami penyebab akar yang menyebabkan kegagalan terjadi. Hal ini membantu perusahaan dalam mengambil langkah-langkah yang tepat untuk mencegah kegagalan serupa di masa depan.
Pertama-tama, analisis kegagalan melibatkan identifikasi penyebab langsung kegagalan peralatan. Tim analisis kegagalan akan melakukan penyelidikan mendalam untuk menentukan apakah kegagalan disebabkan oleh kerusakan mekanis, kegagalan komponen, atau masalah lainnya. Dalam proses ini, berbagai teknik pengujian, seperti pengujian visual, pengujian fisik, atau pengujian laboratorium, dapat digunakan untuk mendapatkan pemahaman yang lebih baik tentang kegagalan tersebut.
Selanjutnya, analisis kegagalan juga melibatkan penentuan faktor-faktor penyebab kegagalan. Ini melibatkan pemeriksaan lebih lanjut untuk mengidentifikasi faktor-faktor yang berkontribusi pada kegagalan, seperti ketidakpatuhan terhadap prosedur operasional, perawatan yang tidak memadai, atau kegagalan desain. Dengan memahami faktor-faktor ini, perusahaan dapat mengambil langkah-langkah perbaikan yang tepat, seperti perubahan prosedur, peningkatan perawatan, atau perubahan desain, untuk mencegah kegagalan serupa di masa depan.
Selain itu, analisis kegagalan juga dapat melibatkan pengumpulan dan analisis data yang relevan. Data yang dikumpulkan, seperti data operasional, data perawatan, atau data pengujian, digunakan untuk melacak dan memahami pola kegagalan yang mungkin terjadi. Dengan melihat data ini secara holistik, perusahaan dapat mengidentifikasi tren kegagalan, mengidentifikasi area yang paling rentan, dan mengambil langkah-langkah preventif yang sesuai.
Terakhir, analisis kegagalan tidak hanya melibatkan upaya perbaikan, tetapi juga pembelajaran. Hasil dari analisis kegagalan dan langkah-langkah perbaikan yang diambil harus didokumentasikan dan dikomunikasikan kepada seluruh tim terkait. Hal ini membantu dalam mentransfer pengetahuan dan pengalaman, sehingga tim dapat belajar dari kegagalan yang terjadi dan mencegah terulangnya kejadian serupa di masa depan. Dengan membangun sistem pembelajaran yang kuat, perusahaan dapat terus meningkatkan keandalan dan kinerja peralatan mereka.
Analisis kegagalan adalah proses penting dalam mengatasi masalah breakdown peralatan. Dengan memahami penyebab akar kegagalan, mengidentifikasi faktor penyebab, menganalisis data yang relevan, dan membangun pembelajaran yang kuat, perusahaan dapat mengambil langkah-langkah yang tepat untuk mencegah kegagalan serupa di masa depan. Melalui upaya analisis kegagalan yang komprehensif, perusahaan dapat meningkatkan keandalan peralatan dan mengoptimalkan kinerja operasional mereka.
Reliability Improvement
Peningkatan keandalan atau reliability improvement adalah suatu pendekatan yang sangat penting dalam upaya perusahaan untuk mengatasi risiko breakdown peralatan yang berulang. Melalui pendekatan ini, perusahaan mencari solusi inovatif dan berkelanjutan untuk meningkatkan keandalan peralatan mereka.
Pertama, untuk meningkatkan keandalan, perusahaan perlu mengidentifikasi faktor penyebab kegagalan yang paling umum. Ini melibatkan analisis data dan pengalaman sebelumnya untuk mengidentifikasi jenis kegagalan yang sering terjadi dan faktor-faktor yang mempengaruhinya. Dengan memahami penyebab umum kegagalan, perusahaan dapat mengambil tindakan yang efektif untuk mengatasi masalah tersebut.
Selanjutnya, perusahaan dapat menerapkan perbaikan berkelanjutan untuk meningkatkan keandalan peralatan. Ini melibatkan melakukan pembaruan pada desain peralatan, penggantian komponen yang kurang handal, atau meningkatkan proses perawatan. Dengan menerapkan perbaikan berkelanjutan, perusahaan dapat mengurangi risiko kegagalan dan meningkatkan masa pakai peralatan secara keseluruhan.
Selain itu, penting untuk mengadopsi pendekatan berbasis data dalam peningkatan keandalan. Perusahaan dapat menggunakan pemantauan dan analisis data real-time untuk mengidentifikasi tanda-tanda awal kegagalan atau performa yang buruk pada peralatan. Dengan memanfaatkan teknologi seperti Internet of Things (IoT) dan analisis data yang cerdas, perusahaan dapat mengambil tindakan proaktif untuk mencegah kegagalan sebelum terjadi.
Terakhir, perusahaan perlu menciptakan budaya perbaikan yang berkelanjutan. Hal ini melibatkan melibatkan seluruh tim dalam usaha meningkatkan keandalan peralatan. Tim dapat diberdayakan untuk mengusulkan perbaikan, membagikan pengetahuan, dan berkolaborasi dalam menyelesaikan masalah. Dengan mendorong budaya perbaikan yang terus-menerus, perusahaan dapat menciptakan lingkungan yang inovatif dan berfokus pada peningkatan keandalan.
Peningkatan keandalan merupakan pendekatan yang penting dalam mengatasi risiko breakdown peralatan yang berulang. Dengan mengidentifikasi faktor penyebab kegagalan, menerapkan perbaikan berkelanjutan, mengadopsi pendekatan berbasis data, dan menciptakan budaya perbaikan yang berkelanjutan, perusahaan dapat mencapai tingkat keandalan yang lebih tinggi. Dengan peralatan yang lebih handal, perusahaan dapat mengoptimalkan produktivitas, mengurangi downtime, dan meningkatkan kepuasan pelanggan. Mari kita terus berinovasi dan meningkatkan keandalan peralatan kita untuk mencapai kesuksesan jangka panjang.
Selamat mencoba! Salam Produktivitas!
Dan Anda bisa terus belajar bersama dengan kami di Jago Kaizen dan Coach Wawang.
Ingin mempelajari secara langsung dan privat tentang TOTAL PRODUCTIVE MAINTENANCE?
Atau Anda ingin mengundang, trainer dan consulting provider?
PT Mitra Prima Produktivitas adalah provider coaching, mentoring, training, dan consulting ternama di Indonesia untuk kinerja Produktivitas dan peningkatan Profitabilitas.