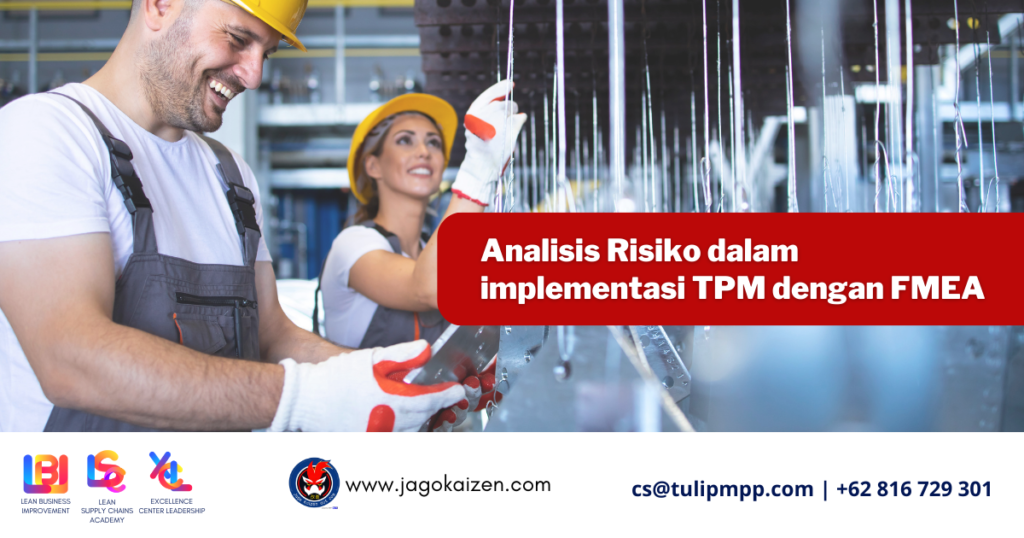
Analisis Risiko dalam implementasi TPM dengan FMEA menggunakan metode Failure Mode and Effects Analysis (FMEA) adalah langkah yang penting dan strategis. FMEA adalah alat analisis yang digunakan untuk mengidentifikasi potensi kegagalan, mengevaluasi dampaknya, dan menentukan langkah-langkah yang diperlukan untuk mencegah atau mengurangi risiko tersebut. Dalam konteks TPM, FMEA dapat membantu tim untuk mengidentifikasi risiko-risiko yang terkait dengan implementasi TPM dan mengembangkan strategi untuk mengatasi risiko-risiko tersebut.
Analisa Resiko Pada Penerapan TPM
Dalam implementasi Total Productive Maintenance (TPM), analisis risiko dengan menggunakan metode Failure Mode and Effects Analysis (FMEA) memainkan peran krusial dalam mengidentifikasi dan mengatasi risiko yang mungkin terjadi. Analisis risiko dalam penerapan TPM membantu tim TPM untuk mengantisipasi dan mengurangi kemungkinan kegagalan yang dapat mempengaruhi kinerja peralatan, mutu produk, dan efisiensi produksi secara keseluruhan.
Dalam analisis risiko dengan FMEA, tim TPM mengidentifikasi kegagalan potensial yang mungkin terjadi dalam implementasi TPM. Misalnya, mereka dapat mengidentifikasi risiko kurangnya pemeliharaan preventif pada mesin, kurangnya partisipasi aktif dari tim dalam perawatan peralatan, atau risiko kesalahan dalam analisis dan perbaikan masalah. Dengan mengidentifikasi risiko-risiko ini, tim dapat memahami ancaman yang mungkin terjadi dan mengambil tindakan pencegahan yang tepat untuk mengurangi risiko tersebut.
Selanjutnya, tim TPM mengevaluasi dampak dari kegagalan potensial terhadap proses produksi, mutu produk, dan kinerja keseluruhan organisasi. Misalnya, mereka mempertimbangkan penurunan produktivitas akibat downtime yang tidak direncanakan, peningkatan tingkat defect yang dapat mempengaruhi kepuasan pelanggan, atau potensi kerugian finansial. Dengan memahami dampak yang mungkin terjadi, tim dapat menetapkan prioritas dan mengarahkan upaya mereka untuk mengatasi risiko yang memiliki dampak paling signifikan.
Setelah mengidentifikasi dan mengevaluasi risiko-risiko, tim TPM mengembangkan langkah-langkah yang diperlukan untuk mencegah atau mengurangi risiko tersebut. Misalnya, mereka merancang program pelatihan yang komprehensif untuk memastikan partisipasi aktif dari seluruh tim dalam implementasi TPM. Selain itu, mereka mengembangkan prosedur yang jelas dan panduan yang mendetail untuk perawatan preventif guna mengurangi kemungkinan kegagalan peralatan. Tim juga menentukan metode pemantauan dan pengendalian yang efektif untuk mendeteksi dini kegagalan atau masalah dalam proses TPM, seperti penggunaan sistem pemantauan real-time atau pemeriksaan berkala yang terjadwal.
Melalui analisis risiko dengan FMEA, tim TPM dapat mengantisipasi dan mengatasi risiko dalam implementasi TPM secara proaktif. Dengan memperhatikan risiko-risiko yang mungkin terjadi, tim dapat mengambil tindakan yang tepat untuk mengurangi kemungkinan kegagalan, meningkatkan kinerja peralatan, dan memastikan mutu produk yang optimal. Analisis risiko dengan FMEA juga membantu tim dalam mengalokasikan sumber daya yang tepat, mengatur prioritas tindakan, dan mengoptimalkan implementasi TPM secara keseluruhan. Dengan demikian, penggunaan FMEA dalam analisis risiko dalam penerapan TPM adalah strategi yang efektif dan penting untuk mencapai keberhasilan dalam meningkatkan kinerja operasional dan mutu produk dalam organisasi.
Tahapan Implementasi FMEA pada TPM
Tahapan dalam analisis FMEA (Failure Mode and Effects Analysis) meliputi identifikasi kegagalan potensial, penentuan tingkat keparahan, penentuan tingkat kemungkinan, penentuan tingkat deteksi, dan penentuan angka risiko (Risk Priority Number/RPN). Dalam konteks Total Productive Maintenance (TPM) pada mesin labelling, tahapan-tahapan FMEA dapat diterapkan sebagai berikut:
- Identifikasi Kegagalan Potensial: Tim TPM melakukan identifikasi semua potensi kegagalan yang mungkin terjadi pada mesin labelling. Contohnya, kegagalan potensial dapat termasuk kerusakan pada rol pemberi label, kesalahan pada sensor pengukur, atau kegagalan pada sistem kontrol suhu.
- Penentuan Tingkat Keparahan: Tim mengevaluasi tingkat keparahan dampak yang mungkin terjadi akibat setiap kegagalan potensial. Misalnya, kegagalan pada rol pemberi label dapat menyebabkan kesalahan dalam penempelan label, yang berpotensi menghasilkan produk cacat atau mengurangi kualitas produk.
- Penentuan Tingkat Kemungkinan: Tim mengevaluasi tingkat kemungkinan kejadian kegagalan potensial. Sebagai contoh, kemungkinan kerusakan pada sensor pengukur dapat dipengaruhi oleh frekuensi penggunaan, kondisi lingkungan, atau kebiasaan pengoperasian mesin.
- Penentuan Tingkat Deteksi: Tim mengevaluasi tingkat kemampuan dalam mendeteksi kegagalan potensial sebelum menyebabkan dampak yang signifikan. Contohnya, dengan adanya sistem pemantauan yang baik dan pengujian berkala, kegagalan pada sistem kontrol suhu dapat dideteksi sebelum menyebabkan penurunan kualitas label atau kerusakan mesin.
- Penentuan Angka Risiko (RPN): Tim mengalikan tingkat keparahan, kemungkinan, dan deteksi untuk setiap kegagalan potensial untuk mendapatkan angka Risiko Priority Number (RPN). RPN membantu tim dalam menentukan prioritas untuk tindakan perbaikan yang perlu dilakukan. Kegagalan dengan RPN yang tinggi menjadi prioritas untuk mendapatkan perhatian lebih dalam implementasi TPM.
Contoh implementasi FMEA dalam TPM mesin labelling adalah ketika tim TPM mengidentifikasi kegagalan potensial pada sistem kontrol suhu. Mereka menentukan tingkat keparahan dampak kegagalan tersebut dengan tingkat tinggi karena dapat mengakibatkan kerusakan label dan produk yang buruk. Selanjutnya, mereka mengevaluasi tingkat kemungkinan kejadian kegagalan dengan tingkat sedang karena adanya sistem pemantauan suhu yang cermat. Tingkat deteksi dinyatakan tinggi karena adanya sensor suhu yang sensitif dan alarm yang aktif. Dengan mengalikan tingkat keparahan, kemungkinan, dan deteksi, tim mendapatkan RPN yang tinggi. Oleh karena itu, tim akan mengutamakan perbaikan pada sistem kontrol suhu sebagai prioritas utama dalam upaya implementasi TPM pada mesin labelling.
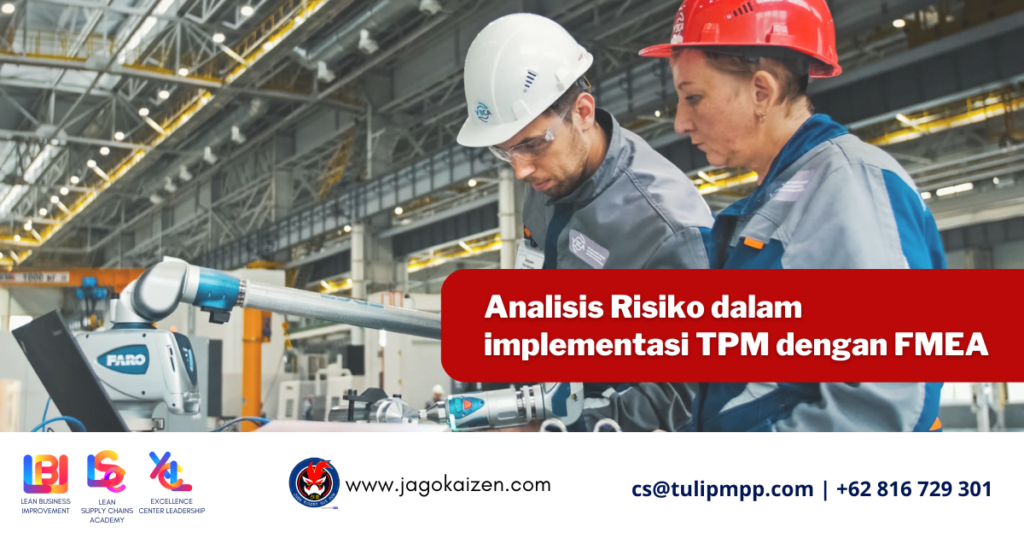
Keuntungan Penerapan FMEA pada Implementasi TPM
Penerapan metode Failure Mode and Effects Analysis (FMEA) dalam implementasi Total Productive Maintenance (TPM) memiliki sejumlah keuntungan yang signifikan. FMEA membantu tim TPM untuk mengidentifikasi dan mengatasi risiko yang terkait dengan operasi peralatan dan proses produksi. Berikut adalah beberapa keuntungan penerapan FMEA dalam implementasi TPM:
- Identifikasi Risiko Potensial: Dengan menggunakan FMEA, tim TPM dapat mengidentifikasi kegagalan potensial yang mungkin terjadi pada peralatan dan proses produksi. Dengan mengetahui risiko-risiko ini, tim dapat mengambil tindakan preventif yang tepat untuk mengurangi kemungkinan terjadinya kegagalan dan menghindari dampak negatifnya terhadap mutu produk dan efisiensi produksi.
- Prioritas Tindakan Perbaikan: Melalui analisis risiko dengan FMEA, tim TPM dapat menetapkan prioritas tindakan perbaikan yang harus diambil. Dengan mengevaluasi tingkat keparahan, kemungkinan, dan deteksi risiko, tim dapat mengidentifikasi risiko yang memiliki dampak dan kemungkinan terbesar. Hal ini memungkinkan tim untuk mengarahkan sumber daya dan upaya mereka pada penanganan risiko-risiko yang paling kritis dan mengurangi kemungkinan terjadinya kegagalan yang signifikan.
- Pencegahan Kegagalan: Penerapan FMEA dalam implementasi TPM memungkinkan tim untuk mengambil tindakan preventif yang efektif. Dengan menganalisis penyebab potensial kegagalan, tim dapat merancang dan mengimplementasikan perawatan preventif yang sesuai. Ini dapat termasuk jadwal pemeliharaan teratur, pelatihan operator, atau perbaikan desain peralatan untuk mengurangi kemungkinan terjadinya kegagalan.
- Peningkatan Efisiensi dan Produktivitas: Dengan mengidentifikasi dan mengatasi risiko potensial, implementasi TPM menjadi lebih efisien dan produktif. Downtime yang tidak direncanakan akibat kegagalan peralatan dapat dikurangi secara signifikan, sehingga meningkatkan waktu operasional dan output produksi. Selain itu, dengan menghindari kerusakan peralatan dan cacat produk, tingkat efisiensi dan kualitas produk dapat meningkat secara keseluruhan.
- Peningkatan Keamanan dan Keselamatan: FMEA juga membantu dalam mengidentifikasi risiko terkait dengan keamanan dan keselamatan kerja. Dengan mengevaluasi potensi kegagalan yang dapat membahayakan operator atau lingkungan kerja, tim TPM dapat mengambil langkah-langkah pencegahan yang tepat untuk melindungi keselamatan dan kesejahteraan pekerja.
Selamat mencoba! Salam Produktivitas!
Dan Anda bisa terus belajar bersama dengan kami di Jago Kaizen dan Coach Wawang.
Ingin mempelajari secara langsung dan privat tentang TOTAL PRODUCTIVE MAINTENANCE?
Atau Anda ingin mengundang, trainer dan consulting provider?
PT Mitra Prima Produktivitas adalah provider coaching, mentoring, training, dan consulting ternama di Indonesia untuk kinerja Produktivitas dan peningkatan Profitabilitas.