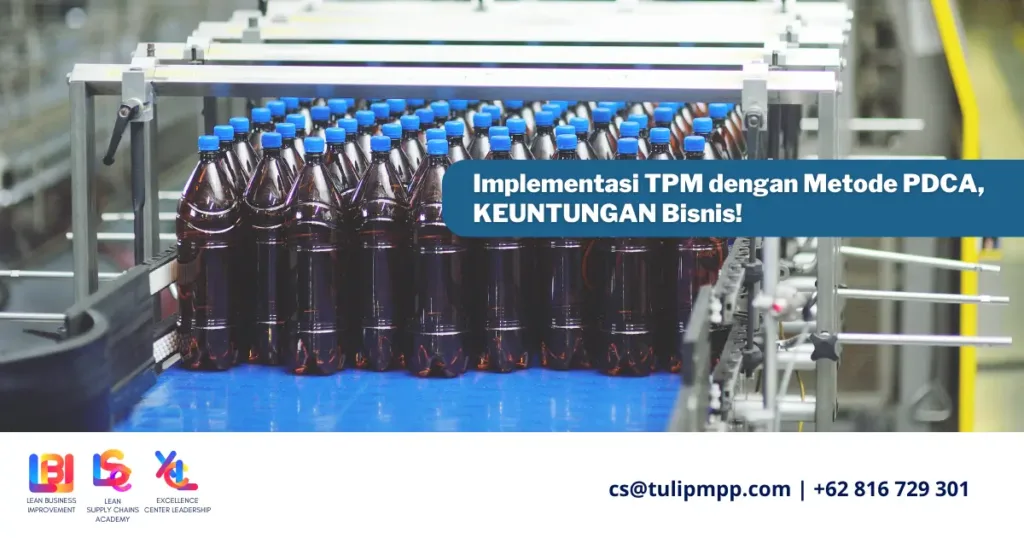
Implementasi TPM dengan Metode PDCA, KEUNTUNGAN Bisnis! Pasti menarik untuk kita bahasa dalam tulisan ini! Ada sudah siap?
Mungkin Anda bertanya-tanya, bisa nggak ya? Bagaimana implementasi Total Productive Maintenance (TPM) dapat meningkatkan keuntungan bisnis dan kekuatan bisnis jangka panjang untuk memenangkan kompetisi bisnis.
Yuk, kita simak bahasn dan contoh kasus bisnisnya!
Strategi Bisnis pada Implementasi TPM
Pertama, mari kita pahami apa itu TPM. Secara sederhana, TPM adalah strategi yang menggabungkan perawatan preventif, perbaikan, dan peningkatan efisiensi untuk memastikan sistem produksi berjalan optimal. Dalam TPM, seluruh anggota organisasi terlibat, mulai dari manajemen hingga operator lini produksi.
Nah, berikut beberapa cara Implementasi TPM dengan Metode PDCA bisa membantu meningkatkan keuntungan bisnis dan kekuatan bisnis jangka panjang:
- Meningkatkan efisiensi produksi. TPM memfokuskan pada pengurangan waste (limbah) dan downtime (waktu berhenti) dalam proses produksi. Hal ini akan meningkatkan produktivitas dan efisiensi, yang pada akhirnya berdampak positif pada keuntungan bisnis.
- Mengurangi biaya perawatan. Dengan melakukan perawatan preventif, biaya perawatan yang tidak terduga bisa ditekan. Hal ini juga mengurangi resiko kegagalan peralatan dan memperpanjang umur peralatan, sehingga menghemat biaya penggantian.
- Meningkatkan kualitas produk. TPM memastikan bahwa setiap elemen dalam sistem produksi berjalan dengan baik, sehingga menghasilkan produk dengan kualitas yang lebih tinggi dan konsisten. Produk berkualitas tinggi akan menarik lebih banyak pelanggan dan mempertahankan loyalitas mereka.
- Meningkatkan keterlibatan karyawan. TPM melibatkan seluruh anggota organisasi dalam proses perawatan dan peningkatan efisiensi. Keterlibatan ini menciptakan budaya kerja yang lebih baik dan meningkatkan kepuasan karyawan, yang pada akhirnya berdampak positif pada bisnis.
- Mempersiapkan bisnis untuk kompetisi. Dalam dunia bisnis yang kompetitif, perusahaan yang efisien dan mampu menghasilkan produk berkualitas tinggi akan lebih unggul. TPM membantu perusahaan dalam hal ini dengan menciptakan sistem produksi yang lebih kuat dan tangguh.
Jadi, implementasi TPM dapat meningkatkan keuntungan bisnis dan kekuatan bisnis jangka panjang melalui peningkatan efisiensi, pengurangan biaya perawatan, peningkatan kualitas produk, dan keterlibatan karyawan yang lebih baik. Semua ini akan mempersiapkan perusahaan untuk memenangkan kompetisi bisnis. Semoga informasi ini bermanfaat untuk Anda! Jangan ragu untuk mengajukan pertanyaan lebih lanjut jika Anda ingin mengetahui lebih banyak tentang TPM.
“Raih keberhasilan Anda dalam implementasi Total Productive Maintenance bersama Senior TPM Consultant terakriditasi, dan optimalisasi kinerja bisnismu dengan solusi terbaik!”
TPM Implementasi dan Ketahanan Biaya
Berikut ini adalah contoh sederhana untuk menggambarkan bagaimana aspek-aspek TPM dapat memberikan dampak keuntungan secara pelaporan keuangan dan keuntungan. Angka-angka ini hanya contoh dan bisa berbeda untuk setiap perusahaan.
Misalkan ada sebuah perusahaan yang memproduksi sepatu dengan data berikut:
- Biaya produksi per pasang sepatu: Rp100.000
- Harga jual per pasang sepatu: Rp150.000
- Jumlah produksi sebelum TPM: 10.000 pasang sepatu per bulan
Setelah menerapkan TPM, perusahaan tersebut berhasil mencapai perbaikan sebagai berikut:
- Efisiensi produksi meningkat 10%
- Biaya perawatan berkurang 20%
- Retur produk berkurang 5% (kualitas produk meningkat)
Mari kita hitung dampaknya pada keuntungan perusahaan:
- Dampak peningkatan efisiensi produksi: Jumlah produksi baru: 10.000 + (10.000 x 10%) = 11.000 pasang sepatu per bulan Keuntungan tambahan: 1.000 pasang sepatu x (Rp150.000 – Rp100.000) = Rp50.000.000
- Dampak pengurangan biaya perawatan: Misalkan biaya perawatan awal per bulan: Rp10.000.000 Penghematan biaya perawatan: Rp10.000.000 x 20% = Rp2.000.000
- Dampak peningkatan kualitas produk (retur berkurang): Jumlah retur awal: 10.000 x 5% = 500 pasang sepatu Jumlah retur baru: 11.000 x (5% – 5%) = 0 pasang sepatu Keuntungan tambahan: 500 pasang sepatu x (Rp150.000 – Rp100.000) = Rp25.000.000
Total keuntungan tambahan per bulan: Rp50.000.000 (efisiensi) + Rp2.000.000 (biaya perawatan) + Rp25.000.000 (kualitas) = Rp77.000.000
Dari contoh di atas, setelah menerapkan TPM, perusahaan tersebut berhasil meningkatkan keuntungannya sebesar Rp77.000.000 per bulan. Tentu saja, angka-angka ini hanya contoh dan bisa berbeda tergantung pada situasi dan skala perusahaan. Namun, contoh ini menunjukkan bagaimana TPM dapat memberikan dampak positif pada keuntungan perusahaan. Semoga contoh ini membantu menjelaskan konsepnya! Jika ada pertanyaan lebih lanjut, jangan ragu untuk bertanya.
Contoh Kasus Perusahaan X dengan Keuntungannya
Bahasan kita lanjutkan pada contoh Implementasi TPM dengan Metode PDCA sebagai tindakan di lantai kerja yang bisa memberikan ketiga dampak yang disebutkan sebelumnya, yaitu peningkatan efisiensi, pengurangan biaya perawatan, dan peningkatan kualitas produk. Kami akan menggunakan metode PDCA (Plan-Do-Check-Act) untuk menjelaskan contoh ini agar mudah dipahami.
Ini adalah contoh kasus keberhasilan penerapan KAIZEN Blitz terkait Implementasi TPM di salah satu klien kami Perusahaan X memproduksi komponen elektronik dengan kondisi awal:
- Waktu siklus produksi: 60 detik per komponen
- Biaya perawatan per bulan: Rp15.000.000
- Tingkat cacat produk: 3%
1. Peningkatan Efisiensi Produksi
Plan: Identifikasi area yang menyebabkan waste dan waktu henti pada proses produksi.
Do: Lakukan tindakan seperti pelatihan operator, penyederhanaan proses, dan penataan ulang area kerja untuk mengurangi waktu siklus produksi.
Check: Evaluasi hasil tindakan yang telah diambil. Misalnya, setelah tindakan tersebut, waktu siklus produksi berkurang menjadi 54 detik per komponen (penurunan 10%).
Act: Standarisasi proses yang telah ditingkatkan dan terus evaluasi untuk peningkatan lebih lanjut.
Dampak: Dengan penurunan waktu siklus 10%, jumlah produksi per jam akan meningkat sebesar 10% pula.
2. Pengurangan Biaya Perawatan
Plan: Kaji jadwal perawatan yang ada dan tentukan bagaimana perawatan preventif bisa lebih efektif.
Do: Terapkan perawatan preventif yang melibatkan operator, seperti pembersihan rutin dan pelumasan peralatan. Misalkan biaya perawatan preventif ini sebesar Rp2.000.000 per bulan.
Check: Evaluasi dampak dari perawatan preventif ini. Misalnya, biaya perawatan yang tidak terduga berkurang dari Rp15.000.000 menjadi Rp10.000.000.
Act: Standarisasi jadwal perawatan preventif dan terus evaluasi untuk peningkatan lebih lanjut.
Dampak: Biaya perawatan berkurang dari Rp15.000.000 menjadi Rp12.000.000 (Rp10.000.000 + Rp2.000.000) per bulan, atau penghematan sebesar Rp3.000.000.
3. Peningkatan Kualitas Produk
Plan: Identifikasi penyebab cacat produk dan tentukan cara untuk mengurangi tingkat cacat.
Do: Lakukan tindakan seperti pelatihan operator dan peningkatan peralatan untuk mengurangi tingkat cacat produk. Misalkan biaya untuk tindakan ini sebesar Rp5.000.000.
Check: Evaluasi hasil tindakan yang telah diambil. Misalnya, tingkat cacat produk berkurang dari 3% menjadi 1,5% (penurunan 50%).
Act: Standarisasi proses yang telah ditingkatkan dan terus evaluasi untuk peningkatan lebih lanjut.
Dampak: Dengan penurunan tingkat cacat produk dari 3% menjadi 1,5%, jumlah produk cacat akan berkurang. Misalkan perusahaan memproduksi 10.000 komponen per bulan, maka jumlah produk cacat akan berkurang dari 300 (3% x 10.000) menjadi 150 (1,5% x 10.000) komponen.
Jadi, melalui implementasi metode PDCA dalam TPM, perusahaan X berhasil mencapai peningkatan efisiensi produksi sebesar 10%, pengurangan biaya perawatan sebesar Rp3.000.000 per bulan, dan peningkatan kualitas produk yang ditunjukkan oleh penurunan tingkat cacat produk sebesar 50%. Dalam jangka panjang, perbaikan ini akan meningkatkan keuntungan dan daya saing perusahaan di pasar.
Semoga contohImplementasi TPM dengan Metode PDCA dapat membantu menjelaskan bagaimana metode PDCA diterapkan dalam TPM untuk meningkatkan efisiensi, mengurangi biaya perawatan, dan meningkatkan kualitas produk. Jangan ragu untuk mengajukan pertanyaan lebih lanjut jika Anda ingin mengetahui lebih banyak tentang topik ini. Selamat mencoba!
Selamat mencoba dan sukses selalu! Salam Produktivitas!
Dan Anda bisa terus belajar bersama dengan kami di Jago Kaizen dan Coach Wang.
Ingin mempelajari secara langsung dan privat dari Senior Konsultan TOTAL PRODUCTIVE MAINTENANCE?
Anda ingin mengundang trainer atau consulting provider?
PT Mitra Prima Produktivitas adalah provider coaching, mentoring, training, dan consulting ternama di Indonesia untuk kinerja Produktivitas dan peningkatan Profitabilitas.
Bersama Coach Wang