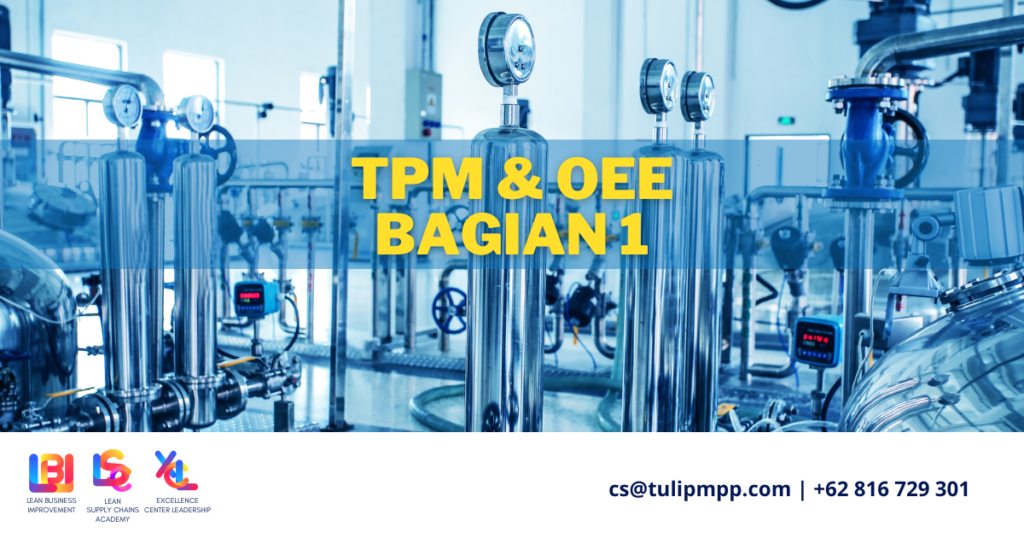
TPM dan OEE (Overall Equipment Effectiveness) bekerja sama untuk menyediakan metrik yang komprehensif dalam mengukur efektivitas keseluruhan mesin dan peralatan kerja. Dengan mengintegrasikan prinsip-prinsip TPM dan indikator kinerja OEE, perusahaan dapat mengidentifikasi area yang memerlukan perbaikan dan mengimplementasikan strategi yang tepat. Hasilnya, perusahaan akan mampu meningkatkan produktivitas, mengurangi downtime, dan mencapai keunggulan kompetitif di pasar.
TPM dan OEE sebagai pengukur efektivitas dan Produktivitas
Total Productive Maintenance (TPM) adalah metodologi yang bertujuan untuk meningkatkan efisiensi dan produktivitas peralatan dalam suatu organisasi. Salah satu metrik yang sering digunakan dalam mengukur keberhasilan TPM adalah Overall Equipment Effectiveness (OEE). Tulisan ini akan membahas hubungan antara TPM dan OEE serta bagaimana mengukur efektivitas keseluruhan peralatan dapat meningkatkan produktivitas di industri pabrik coklat.
TPM dan OEE
OEE adalah metrik yang menggabungkan tiga aspek utama dari efisiensi peralatan: ketersediaan, performa, dan kualitas. Ketersediaan mengacu pada seberapa sering peralatan dapat digunakan saat dibutuhkan, performa mengacu pada seberapa cepat peralatan dapat menghasilkan produk, dan kualitas mengacu pada seberapa banyak produk yang dihasilkan memenuhi spesifikasi yang diharapkan. Dengan mengukur OEE, perusahaan pabrik coklat dapat mengidentifikasi area yang memerlukan perbaikan dan mengevaluasi kemajuan mereka dalam meningkatkan efisiensi peralatan.
Contoh Implementasi TPM dan OEE di Industri Pabrik Coklat.
Sebuah pabrik coklat ingin meningkatkan efisiensi dan produktivitas peralatannya. Manajemen memutuskan untuk mengimplementasikan TPM dan mulai mengukur OEE.
Berikut adalah beberapa langkah yang diambil pabrik coklat untuk mencapai tujuan ini:
- Melakukan pelatihan untuk operator dan teknisi dalam melakukan pemeliharaan mandiri (Autonomous Maintenance) dan mengidentifikasi potensi perbaikan.
- Mengidentifikasi dan mengurangi enam kerugian besar yang mempengaruhi OEE, seperti kegagalan peralatan, penyetelan dan penyesuaian, berhenti sebentar dan gangguan kecil, kecepatan berkurang, cacat proses, dan hasil berkurang.
- Menyusun jadwal pemeliharaan yang terencana (Planned Maintenance) untuk memastikan peralatan selalu dalam kondisi optimal.
- Mengadopsi sistem manajemen kualitas yang menekankan pada pencegahan cacat dan peningkatan proses.
- Melibatkan seluruh organisasi dalam proses perbaikan berkelanjutan, termasuk manajemen puncak, dengan mengadopsi prinsip-prinsip Kaizen.
- Menggunakan teknologi seperti sistem pengumpulan data otomatis dan perangkat lunak analisis untuk melacak kinerja OEE secara real-time, memungkinkan identifikasi cepat dan respons terhadap masalah yang mungkin muncul.
“Dapatkan solusi terbaik untuk meningkatkan kinerja dan hasil produksimu dengan implementasi Total Productive Maintenance bersama Senior TPM Consultant terakriditasi, dan raih kesuksesanmu sebagai pelaku bisnis yang handal!”
Dalam contoh ini, pabrik coklat melihat peningkatan signifikan dalam OEE setelah mengimplementasikan TPM, yang pada akhirnya berdampak pada peningkatan produktivitas dan efisiensi operasional.
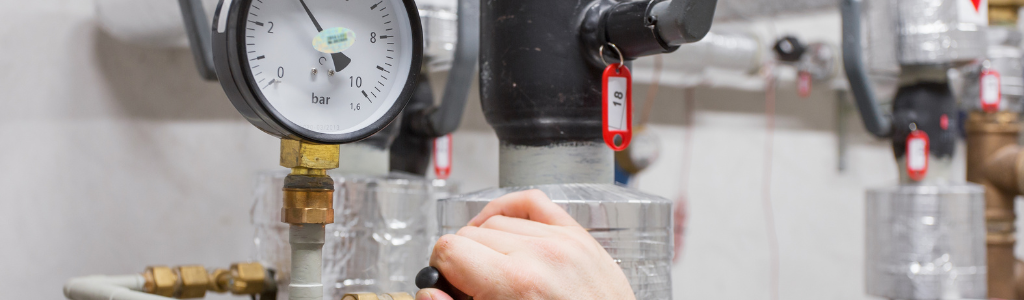
Hasil Implementasi TPM dan OEE di Industri Pabrik Coklat
Setelah menerapkan TPM dan mengukur OEE, pabrik coklat tersebut melihat beberapa peningkatan kinerja, seperti:
- Penurunan downtime peralatan dan peningkatan ketersediaan, yang mengurangi waktu tunggu dan memungkinkan peningkatan output produksi.
- Peningkatan kecepatan dan efisiensi proses produksi, yang berarti lebih banyak produk yang dihasilkan dalam waktu yang lebih singkat.
- Peningkatan kualitas produk, dengan jumlah cacat yang berkurang dan tingkat kepuasan pelanggan yang meningkat.
Kesimpulan:
Total Productive Maintenance (TPM) dan Overall Equipment Effectiveness (OEE) adalah dua konsep yang saling terkait dalam upaya meningkatkan efisiensi dan produktivitas peralatan. Dengan mengimplementasikan TPM dan mengukur OEE, industri pabrik coklat dapat mengidentifikasi area yang memerlukan perbaikan dan mengevaluasi kemajuan mereka dalam meningkatkan efisiensi peralatan. Implementasi TPM dan OEE yang sukses akan menghasilkan peningkatan kinerja, termasuk penurunan downtime peralatan, peningkatan kecepatan proses produksi, dan peningkatan kualitas produk, yang pada akhirnya akan berdampak positif pada produktivitas dan profitabilitas perusahaan.
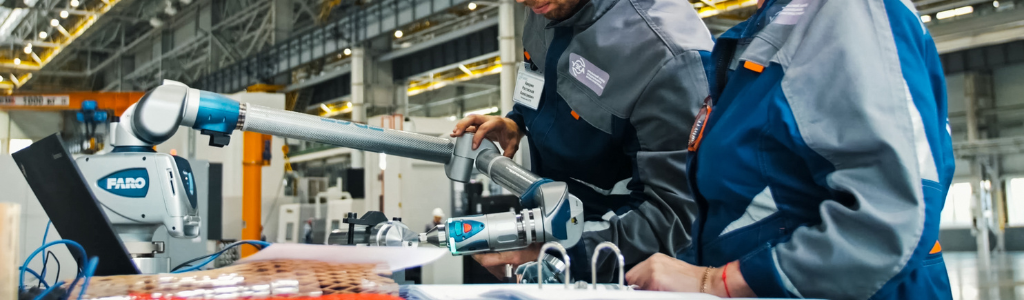
Overall Equipment Effectiveness (OEE)
Overall Equipment Effectiveness (OEE) adalah metrik yang digunakan untuk mengukur efisiensi dan efektivitas peralatan dalam proses produksi. OEE membantu mengidentifikasi area yang memerlukan perbaikan dan mengevaluasi sejauh mana peralatan digunakan secara optimal. OEE dihitung dengan mengalikan tiga komponen: ketersediaan, kinerja, dan kualitas.
Availability atau Ketersediaan: Merupakan rasio antara waktu operasi yang sebenarnya dengan waktu operasi yang direncanakan. Ketersediaan mengukur sejauh mana peralatan tersedia untuk produksi.
Rasio Ketersediaan (AR) = (Waktu Operasi Sebenarnya / Waktu Operasi yang Direncanakan) x 100
Performance atau Kinerja: Merupakan rasio antara output aktual dan output teoritis yang seharusnya dihasilkan dalam waktu operasi yang sebenarnya. Kinerja mengukur seberapa efisien peralatan beroperasi.
Rasio Kinerja (PR) = (Output Aktual / Output Teoritis) x 100
Quality atau Kualitas: Merupakan rasio antara jumlah produk yang memenuhi standar kualitas dengan jumlah produk yang dihasilkan. Kualitas mengukur sejauh mana produk yang dihasilkan memenuhi standar yang ditetapkan.
Rasio Kualitas (QR) = (Produk yang Memenuhi Standar / Produk yang Dihasilkan) x 100
OEE = Ketersediaan x Kinerja x Kualitas = AR x PR x QR
Six Big Losses
Six Big Losses adalah enam penyebab utama yang mempengaruhi OEE. Mereka terbagi menjadi tiga kategori: kehilangan ketersediaan, kehilangan kinerja, dan kehilangan kualitas.
- Equipment Failure (Kegagalan Peralatan). Gangguan yang disebabkan oleh kerusakan peralatan atau sistem yang mempengaruhi ketersediaan.
- Setup and Adjustments (Pengaturan dan Penyesuaian). Waktu yang hilang karena perubahan alat atau penyesuaian peralatan yang mempengaruhi ketersediaan.
- Idling and Minor Stops (Menganggur dan Henti Minor). Gangguan singkat yang mempengaruhi kinerja, seperti penyumbatan atau masalah pemasok.
- Reduced Speed (Kecepatan Berkurang). Kecepatan produksi yang lebih rendah dari kapasitas peralatan yang mempengaruhi kinerja.
- Process Defects (Kecacatan Proses). Produk cacat yang dihasilkan selama proses produksi yang mempengaruhi kualitas.
- Reduced Yield (Hasil Berkurang). Produk yang tidak memenuhi standar kualitas pada awal proses produksi yang mempengaruhi kualitas.
Contoh perhitungan OEE
Misalkan sebuah mesin dalam pabrik coklat memiliki kapasitas produksi sebanyak 480 unit per jam. Berikut adalah data yang diperoleh dari mesin tersebut:
- Waktu Kerja: 480 menit
- Waktu henti mesin (downtime): 30 menit
- Output yang dihasilkan: 450 unit
- Unit cacat: 10 unit
Untuk menghitung OEE, kita perlu menentukan ketiga komponen utamanya: Ketersediaan, Kinerja, dan Kualitas.
- Ketersediaan, Availability Rate. Ketersediaan mesin dihitung dengan membagi waktu kerja efektif (waktu kerja dikurangi downtime) dengan waktu kerja total. AR = (Waktu Kerja Efektif) / (Waktu Kerja Total) x 100
- Kinerja, Performance Rate. Kinerja mesin dihitung dengan membagi output aktual yang dihasilkan mesin dengan output yang seharusnya dihasilkan dalam waktu kerja efektif. PR = (Output Aktual) / (Output yang Seharusnya) x 100
- Kualitas, Quality Rate. Kualitas mesin dihitung dengan membagi jumlah unit yang diproduksi tanpa cacat dengan jumlah unit total yang diproduksi. QR = (Unit Tanpa Cacat) / (Unit Total) x 100
Menggunakan data yang diberikan:
AR = ((480 – 30) / 480) x 100 = 93,75%
PR = (450 / (480 – 30)) x 100 = 100%
QR = (450 – 10) / 450 x 100 = 97,78%
OEE = AR x PR X QR = 93,75% x 100% x 97,78% = 91,76%
Dalam contoh ini, OEE mesin produksi adalah 91,76%, yang menunjukkan bahwa mesin tersebut bekerja dengan efisiensi yang tinggi. Namun, masih ada ruang untuk perbaikan, terutama dalam hal mengurangi downtime dan meningkatkan kualitas produk yang dihasilkan. Melakukan analisis Six Big Losses akan membantu mengidentifikasi area yang memerlukan perbaikan dan mengoptimalkan efisiensi peralatan.
Misalkan kita memiliki mesin pengemas coklat di sebuah pabrik coklat dengan kapasitas produksi sebanyak 800 unit per jam. Berikut adalah data yang diperoleh dari mesin tersebut, termasuk Six Big Losses:
- Waktu Kerja: 480 menit
- Breakdown Loss (Kerusakan Peralatan): 40 menit
- Setup and Adjustment Loss (Pengaturan dan Penyesuaian): 30 menit
- Idling and Minor Stops Loss (Menganggur dan Henti Kecil): 20 menit
- Reduced Speed Loss (Kecepatan Berkurang): 50 menit (Kapasitas mesin menurun menjadi 600 unit per jam selama periode ini)
- Process Defects Loss (Kerusakan Proses): 80 unit cacat
- Reduced Yield Loss (Hasil Berkurang): 30 unit cacat selama startup dan shutdown
Menggunakan data yang diberikan:
Waktu Kerja Efektif = Waktu Kerja – Breakdown Loss – Setup and Adjustment Loss
Waktu Kerja Efektif = 480 menit – 40 menit – 30 menit = 410 menit
Output yang seharusnya dihasilkan = Kapasitas Mesin x Waktu Kerja Efektif
Output yang seharusnya dihasilkan = 800 unit/jam x 410 menit / 60 menit/jam = 5,467 unit
Output aktual = Output yang seharusnya dihasilkan – Reduced Speed Loss
Output aktual = 5,467 unit – (50 menit x 200 unit/jam) / 60 menit/jam = 4,967 unit
Total Unit yang diproduksi = Output aktual + Process Defects Loss + Reduced Yield Loss
Total Unit yang diproduksi = 4,967 unit + 80 unit + 30 unit = 5,077 unit
Unit tanpa cacat = Total Unit yang diproduksi – Process Defects Loss – Reduced Yield Loss
Unit tanpa cacat = 5,077 unit – 80 unit – 30 unit = 4,967 unit
Ketersediaan = (Waktu Kerja Efektif) / (Waktu Kerja) x 100
Ketersediaan = (410 menit) / (480 menit) x 100 = 85,42%
Kinerja = (Output Aktual) / (Output yang Seharusnya) x 100
Kinerja = (4,967 unit) / (5,467 unit) x 100 = 90,85%
Kualitas = (Unit Tanpa Cacat) / (Total Unit yang diproduksi) x 100
Kualitas = (4,967 unit) / (5,077 unit) x 100 = 97,83%
OEE = Ketersediaan x Kinerja x Kualitas
OEE = 85,42% x 90,85% x 97,83% = 76,01%
Dalam contoh ini, OEE mesin pengemas coklat adalah 76,01%, yang menunjukkan bahwa mesin tersebut bekerja dengan efisiensi yang moderat. Melakukan analisis Six Big Losses akan membantu mengidentifikasi area yang memerlukan perbaikan dan mengoptimalkan efisiensi peralatan.
Equipment Failure Reduction
Equipment Failure (Kegagalan Peralatan) merupakan salah satu dari Six Big Losses dalam Overall Equipment Effectiveness (OEE). Kegagalan peralatan meliputi kerusakan mesin dan peralatan yang menyebabkan downtime yang tidak dijadwalkan.
Downtime adalah periode di mana mesin atau peralatan tidak beroperasi atau tidak produktif karena alasan yang direncanakan atau tidak direncanakan.
Breakdown, di sisi lain, adalah kejadian spesifik di mana mesin atau peralatan mengalami kerusakan atau kegagalan, sehingga menyebabkan downtime yang tidak direncanakan. Jadi, breakdown adalah salah satu penyebab downtime, tetapi downtime juga bisa disebabkan oleh perawatan yang direncanakan, pergantian alat, atau gangguan lain yang tidak terkait dengan kerusakan mesin.
Perlu dicatat agar lebih paham: DOWNTIME adalah durasi waktu terjadinya BREAKDOWN atau failure.
Mengurangi kegagalan peralatan dapat meningkatkan efisiensi mesin dan mengurangi waktu henti. Berikut adalah contoh tindakan yang dapat diambil dan metrik yang relevan untuk mengurangi kegagalan peralatan:
Contoh: Sebuah perusahaan pabrik coklat memiliki mesin pengemas yang mengalami kegagalan peralatan sebanyak 4 kali dalam sebulan, dengan total downtime sebesar 200 menit.
Tindakan 1: Peningkatan Pemeliharaan Preventif
Metrik: Jumlah pemeliharaan preventif yang dilakukan per bulan
Contoh: Peningkatan frekuensi pemeliharaan preventif dari 1 kali per bulan menjadi 2 kali per bulan.
Tindakan 2: Pelatihan Operator
Metrik: Jumlah pelatihan yang diikuti oleh operator per kuartal
Contoh: Operator mengikuti pelatihan tentang perawatan dasar mesin dan cara mengatasi gangguan ringan, minimal 1 kali per kuartal.
Tindakan 3: Analisis Penyebab Akar (Root Cause Analysis)
Metrik: Jumlah kegagalan peralatan yang diinvestigasi dan penyebab akar yang diidentifikasi
Contoh: Melakukan analisis penyebab akar pada setiap kegagalan peralatan dan mengidentifikasi area yang memerlukan perbaikan.
Tindakan 4: Penggantian Komponen yang Usang
Metrik: Jumlah komponen yang diganti
Contoh: Mengganti 2 komponen yang usang pada mesin pengemas yang sering mengalami kegagalan.
Dengan mengambil tindakan ini, perusahaan pabrik coklat berhasil mengurangi jumlah kegagalan peralatan dari 4 kali menjadi 2 kali dalam sebulan, dan mengurangi total downtime menjadi 80 menit. Ini merupakan peningkatan signifikan dalam efisiensi mesin dan mengurangi waktu henti yang tidak dijadwalkan.
Setup and Adjustments Time Reduction
Pengurangan waktu setup dan penyesuaian adalah langkah penting dalam meningkatkan efisiensi mesin dan mengurangi downtime. Salah satu metode yang efektif untuk mengurangi waktu setup dan penyesuaian adalah dengan menerapkan pendekatan Single Minute Exchange of Die (SMED).
Single Minute Exchange of Die (SMED) adalah metode lean yang dikembangkan oleh Shigeo Shingo untuk mengurangi waktu setup dan penyesuaian mesin. Tujuannya adalah mengurangi waktu setup menjadi sembilan menit atau kurang (single-digit minute). SMED membantu meningkatkan fleksibilitas, mengurangi downtime, dan meningkatkan produktivitas.
Contoh aktivitas SMED:
- Memisahkan setup internal dan eksternal. Setup internal adalah aktivitas yang harus dilakukan saat mesin berhenti, sedangkan setup eksternal adalah aktivitas yang bisa dilakukan saat mesin masih beroperasi. Misalnya, menyiapkan alat dan bahan untuk pergantian selanjutnya saat mesin sedang beroperasi.
- Mengonversi setup internal menjadi eksternal. Mengubah aktivitas setup internal menjadi eksternal agar sebagian besar proses setup dapat dilakukan sambil mesin beroperasi. Misalnya, menggunakan sistem pengganti cepat untuk mempersiapkan cetakan selanjutnya di luar mesin.
- Meningkatkan efisiensi setup. Mengoptimalkan proses setup dengan mengurangi langkah yang tidak perlu, menggunakan alat bantu, dan melatih operator untuk bekerja lebih efisien.
Untuk menghitung durasi per elemen SMED, Anda perlu menguraikan proses setup saat ini dan mencatat waktu yang dihabiskan untuk setiap aktivitas. Misalkan, proses setup saat ini melibatkan tiga aktivitas:
- Menghentikan mesin dan melepas cetakan lama: 10 menit
- Menyiapkan dan memasang cetakan baru: 30 menit
- Menyesuaikan parameter mesin dan menguji hasil: 20 menit
Total waktu setup saat ini: 10 + 30 + 20 = 60 menit
Setelah menerapkan SMED, Anda akan mencatat waktu yang diperlukan untuk setiap aktivitas yang telah ditingkatkan. Kemudian, bandingkan durasi sebelum dan sesudah implementasi SMED untuk menilai peningkatan yang dicapai.
Misalkan, sebuah perusahaan manufaktur yang memproduksi komponen otomotif menggunakan mesin yang memerlukan setup dan penyesuaian selama 90 menit setiap kali mengganti model komponen. Dalam sebulan, ada 30 kali pergantian model.
Tindakan untuk mengurangi waktu setup dan penyesuaian meliputi:
- Memisahkan setup internal dan eksternal.
- Mengonversi setup internal menjadi eksternal.
- Menggunakan alat pengganti cepat.
Setelah menerapkan tindakan ini, perusahaan berhasil mengurangi waktu setup dan penyesuaian menjadi 45 menit.
Metrik yang digunakan adalah pengurangan waktu setup dan penyesuaian dalam menit:
- Sebelum perbaikan: 90 menit x 30 pergantian = 2700 menit/bulan
- Setelah perbaikan: 45 menit x 30 pergantian = 1350 menit/bulan
Pengurangan waktu setup dan penyesuaian: (2700 – 1350) menit = 1350 menit/bulan (50% pengurangan)
Dengan mengurangi waktu setup dan penyesuaian, perusahaan dapat meningkatkan produktivitas, mengurangi downtime, dan menghasilkan lebih banyak output dalam jangka waktu yang sama.
Selamat mencoba, dan sukses selalu!
Salam Produktivitas!
Dan Anda bisa terus belajar bersama dengan kami di Jago Kaizen dan Coach Wang.
Ingin mempelajari secara langsung dan privat dari Senior Konsultan TOTAL PRODUCTIVE MAINTENANCE?
Anda ingin mengundang trainer atau consulting provider?
PT Mitra Prima Produktivitas adalah provider coaching, mentoring, training, dan consulting ternama di Indonesia untuk kinerja Produktivitas dan peningkatan Profitabilitas.
[Lanjut ke bagian 2 dari 2: TPM & OEE] Dan Anda bisa terus belajar bersama dengan kami di Jago Kaizen dan Coach Wang.